Revolutionising Residential Builds: The Future of 3D-Printed Homes in New Zealand
In recent years, 3D printing has emerged as a revolutionary technology, transforming industries from manufacturing to healthcare with its ability to create complex designs with unparalleled precision and efficiency. This innovative process allows for the layer-by-layer construction of objects, minimizing waste and reducing production time, which has captivated the imagination of entrepreneurs and creators alike. As this technology continues to evolve, one of the most exciting developments is the application of 3D printing in construction—specifically, the printing of entire houses.
Iconic3D is leading a new era in home building. As the first company in New Zealand to construct a 3D-printed show home, the Hamilton-based business is redefining residential construction. Utilising an innovative insulated concrete panel system, Iconic3D is able to reduce build times while enhancing the quality and durability of homes.
Their 3D printed homes are designed to last, taking advantage of the longer lifespan inherent of building in concrete. Offering superior insulation, durability, and climate resilience. Iconic3D walls are engineered to meet and significantly exceed NZ seismic requirements, with test showing a strength almost four times that of its timber alternative.
With the first 3D-printed show home set for completion just 3.5 months after breaking ground, Iconic3D is demonstrating that 3D printing offers a faster, smarter, and more sustainable alternative to traditional construction methods.
After learning about the Iconic3D team have been working on, we had some questions; read on to learn more if you’re also as intrigued about the future on 3D printed homes in New Zealand as we are.
What makes a 3D printed structure/home more climate resilient than a standard build?
Concrete has excellent thermal qualities which is why it has been utilised is countries the world over. A concrete solution creates a comfortable environment due to it’s high thermal mass which regulates building temperature and minimises the effect of temperature extremes, a common issue in New Zealand. More climate resistant, the concrete walls will absorb heat during the days, releasing that slowly including in the cooler night-time periods. Our walls also have greater resilience in floods due to its concrete structure and can protect against flood damage, where its timber alternative would require demolition and rebuilding as seen in flood-prone areas in New Zealand.
Thinking of the first show home currently being built, what parts of the house structure is being built by the 3D printer vs what is still traditional product. i.e. roof?
All structural walls in the home are 3D printed. Traditional timber is used from the ceiling up through the roof structure. We will also utilise the 3D printing for exterior landscaping, which includes a rain garden to retain the properties water runoff.
Your website mentions higher quality, built faster and more climate resilient. How does this match up in terms of cost vs a traditional build of similar size and design?
When you factor in our curved walls and the cost of these in a traditional timber build, our cost is likely more competitive. Speed of construction can also lead to costs savings with getting families into their homes faster, saving costs associated with renting, or double mortgages while their homes are being constructed.
What is the current capacity (and timeframe) for building a new home from scratch in the Christchurch region?
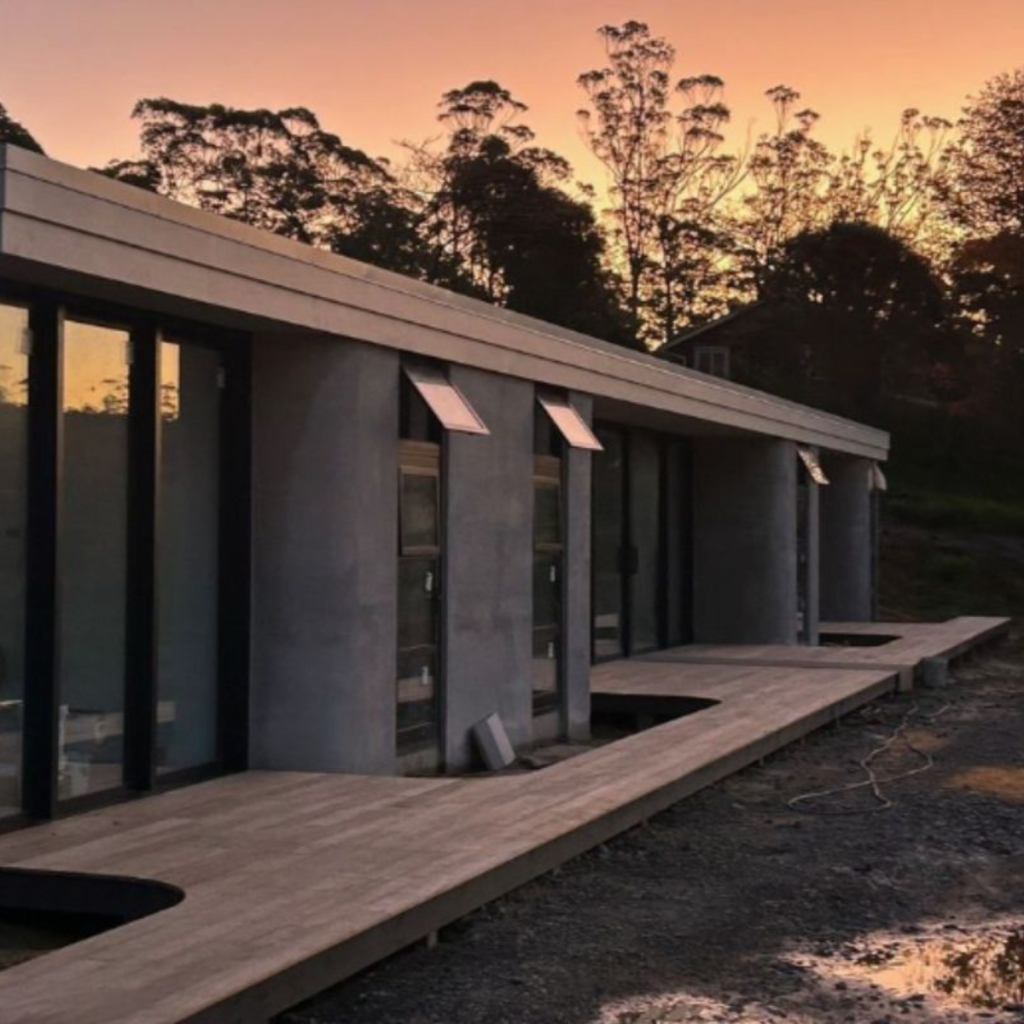
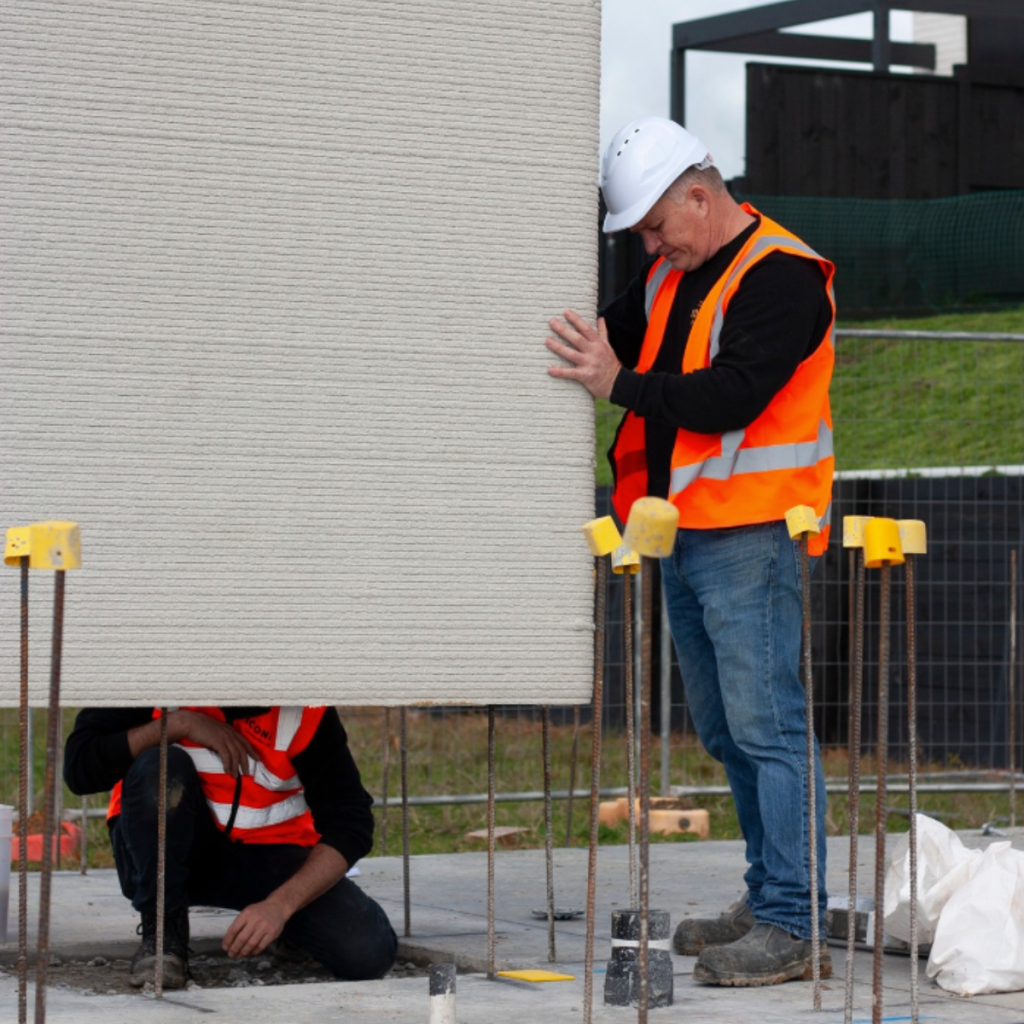
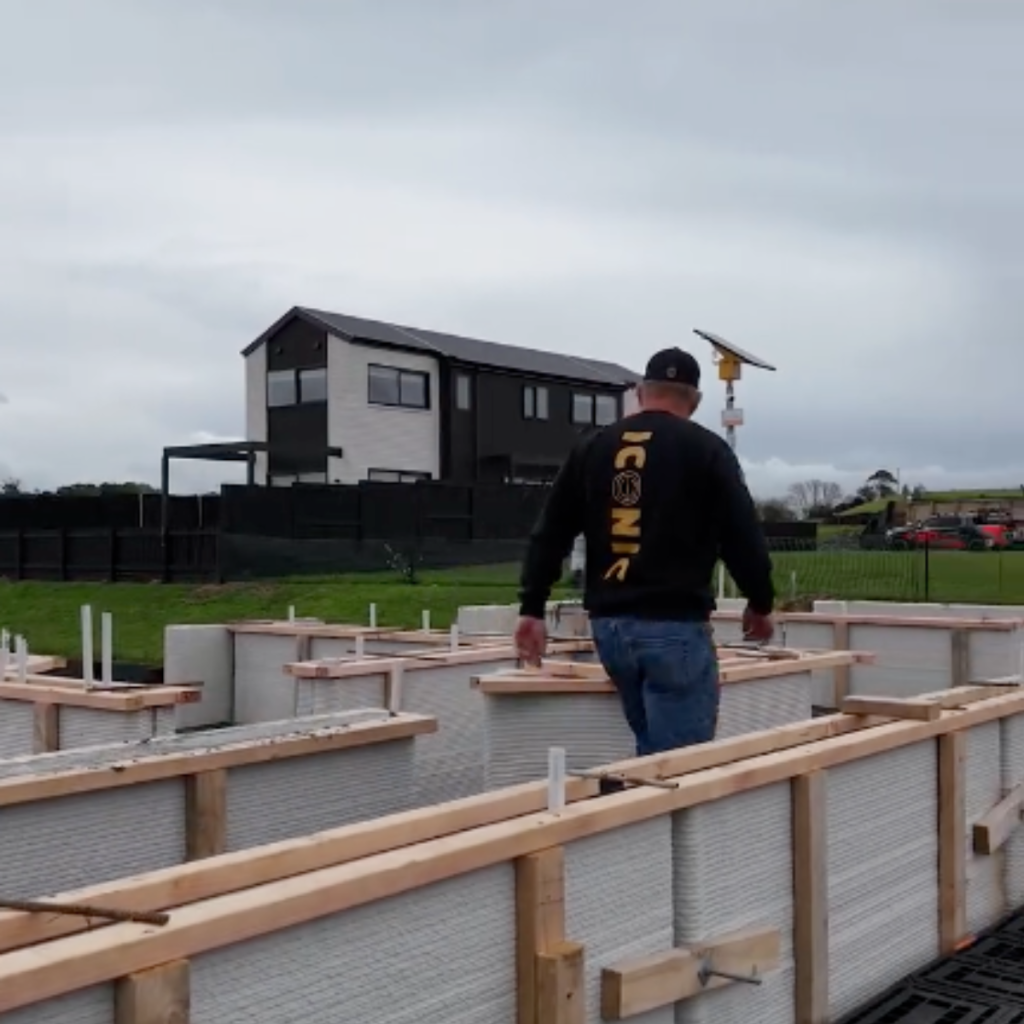
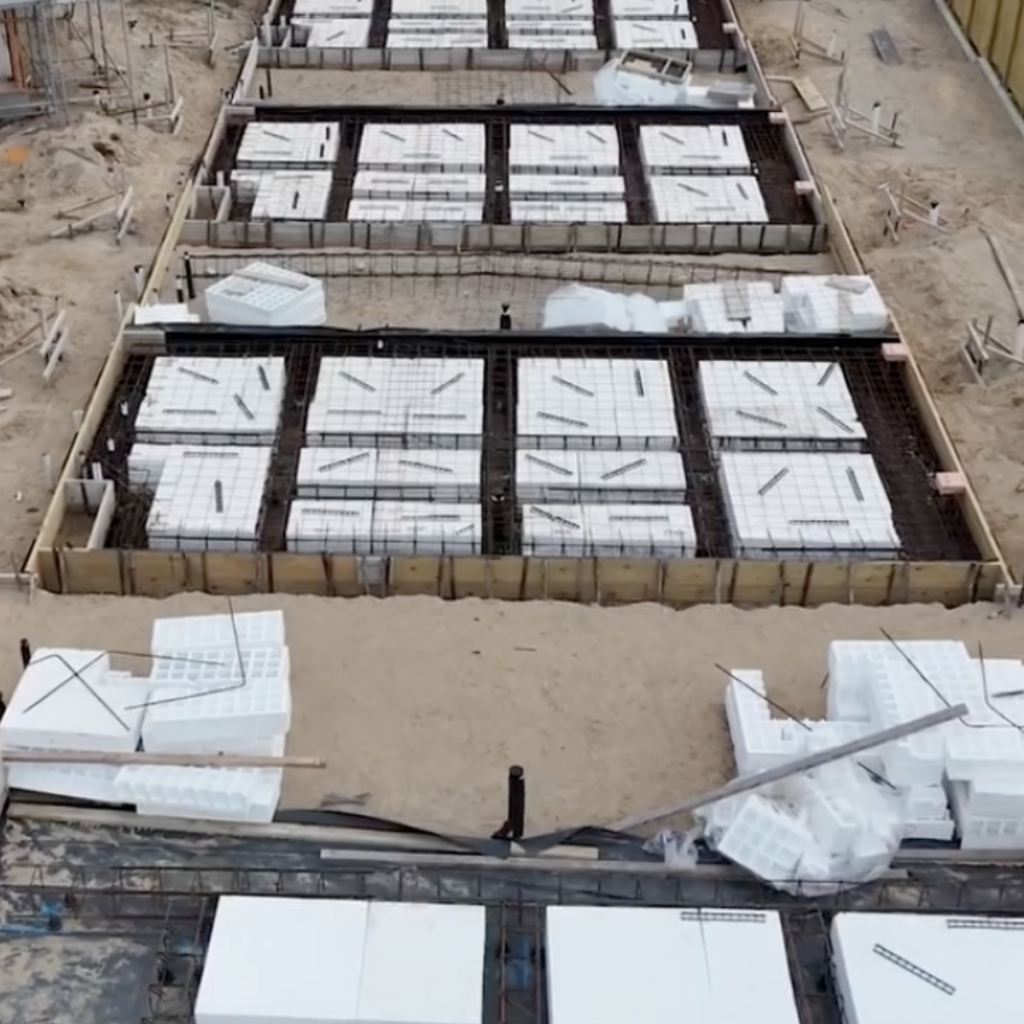
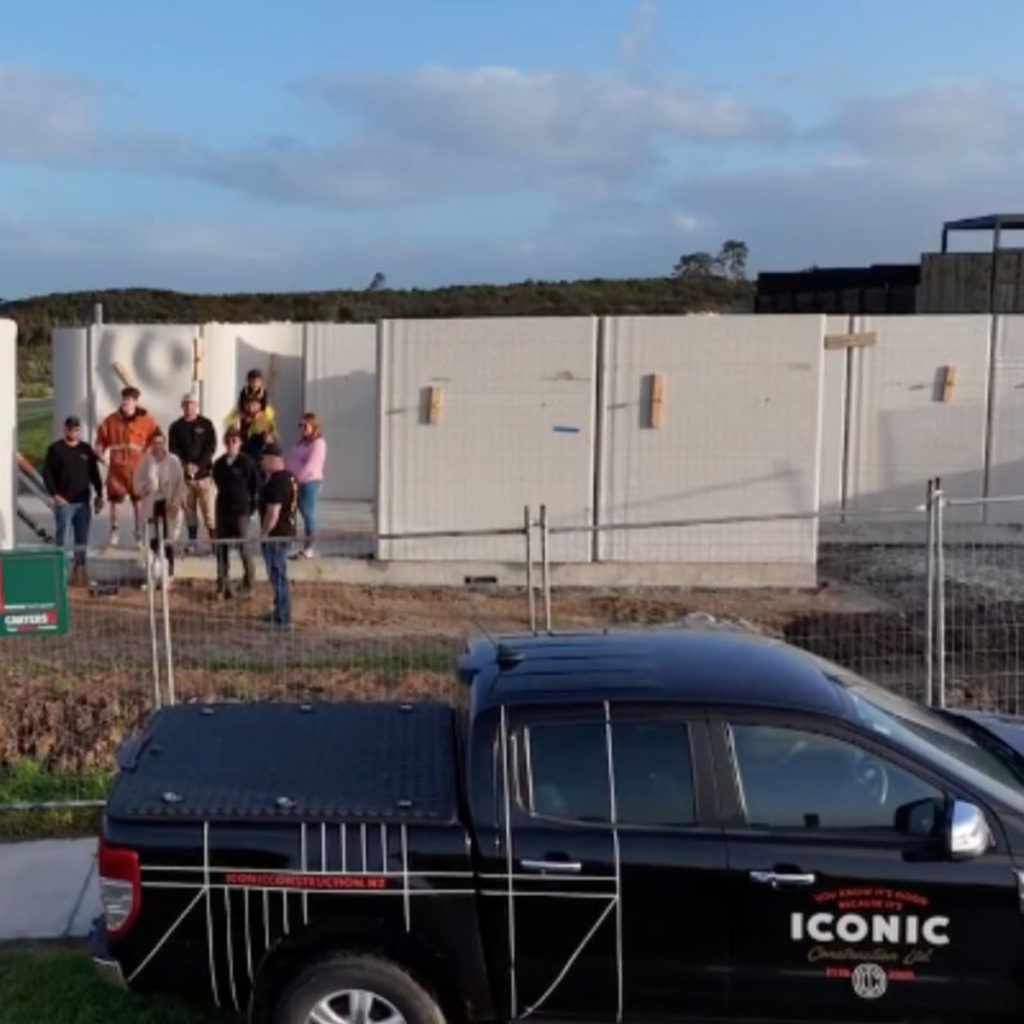